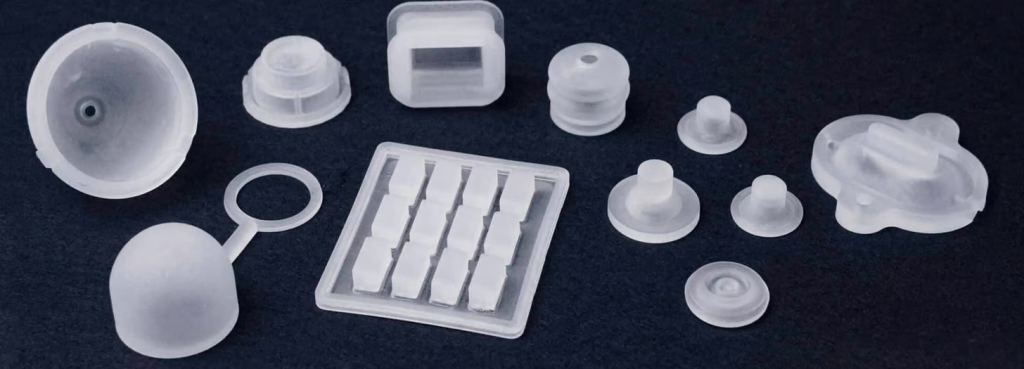
Liquid Silicone Rubber (LSR) has arisen as a flexible and creative material in the new era of 3D printing. Famous for its flexibility, durability, and resistance to outrageous circumstances, LSR opens up additional opportunities in assembling, prototyping, and design. This guide investigates the utilization of LSR in 3D printing, featuring its advantages, highlights, and applications. We will likewise talk about where to purchase the best LSR for your 3D printing projects and close with an outline of its importance in present day innovation.
How is Liquid Silicone Rubber Used in 3D Printing?
Liquid Silicone Rubber is used in 3D printing through a cycle known as Liquid Additive Manufacturing (LAM). This method includes storing layers of liquid silicone rubber, which are then restored utilizing UV light or intensity to make the final item. The LAM cycle and process considers exact control over the material properties and the capacity to make complex calculations that would be troublesome or inconceivable with conventional assembling strategies.
The process starts with a computerized (digital) design, which is cut into thin layers by specific software specialized for this purpose only. These layers guide the 3D printer as it stores the liquid silicone rubber layer by layer. Each layer is restored before the next is added, guaranteeing that the material holds its shape and properties all through the printing system. This strategy is especially helpful for delivering models, custom parts, and little groups of items with high accuracy and repeatability.
Benefits of Using Liquid Silicone Rubber for 3D Printing
Elasticity and Flexibility
LSR is exceptionally adaptable and flexible, making it ideal for making parts that need to curve, stretch, or compress without losing their shape or capability. This property is especially significant in applications like medical gadgets, wearables, and auto parts.
Intricate Detailing
The LAM process considers high accuracy, precision and intricate designs. This capacity is vital for making complex geometries and detailed [patterns that are fundamental in numerous modern and customer applications.
Strength and Durability
LSR is resistant to mileage, UV light, and outrageous temperatures. This durability guarantees that printed parts can endure brutal conditions and delayed use without degrading.
Customization
LSR can be effortlessly colored, customized, and textured to meet explicit requirements. This flexibility empowers manufacturers to make remarkably unique and custom items for different applications.
Biocompatible
LSR is non-toxic and hypoallergenic, making it appropriate for clinical and food-related applications. It tends to be utilized to deliver prosthetics, implants, and other medical gadgets that come into contact with the human body.
Applications of Liquid Silicone Rubber for 3D Printing
Liquid Silicone Rubber (LSR) is widely utilized in the clinical field because of its biocompatibility, flexibility, and durability. In 3D printing, LSR empowers the development of custom prosthetics, implants, and wearable clinical gadgets that exactly match the exceptional physical elements of individual patients. This customization upgrades patient comfort and usefulness, as gadgets like hearing aids, dental implants, and orthopedic backings can be custom-made to perfectly fit.
Moreover, LSR’s hypoallergenic properties make it alright for delayed skin contact, making it ideal for making clinical gadgets that require immediate and consistent communication with the human body.
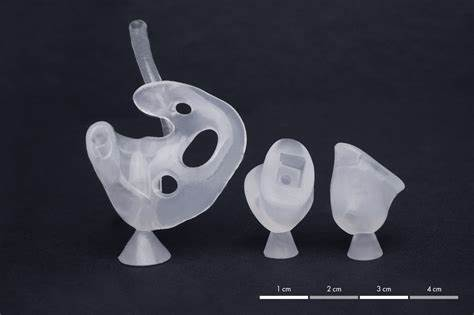
In the auto industry, LSR’s resistance to outrageous temperatures and its strong mechanical properties make it a great material for producing gaskets, seals, and other different parts that need to perform dependably under unforgiving circumstances. 3D printing with LSR considers the quick prototyping and production of complex parts that can endure the afflictions of auto conditions, including exposure to oil, fuel, and outrageous temperatures. This ability speeds up the design and testing stages as well as considers the making of profoundly definite and exact parts that work on the general execution and security of vehicles.
LSR’s flexibility stretches out to consumer devices, where it is used to make protective cases, adaptable connectors, and seals. The accuracy of 3D printing with LSR empowers the production of uniquely fit cases that offer prevalent insurance for gadgets, for example, cell phones, tablets, and wearables. The material’s resistance to mileage, joined with its capacity to absorb shocks, guarantees that electronic gadgets remain defended from day to day influences and natural variables.
Furthermore, the stylish conceivable outcomes of LSR, remembering its accessibility for different tones and gets done, take into consideration the development of outwardly engaging and practical accessories that upgrade the user experience.
Features of the Best LSR for 3D Printing
While choosing Liquid Silicone Rubber (LSR) for 3D printing, a few crucial features guarantee ideal performance and nature of the end result.
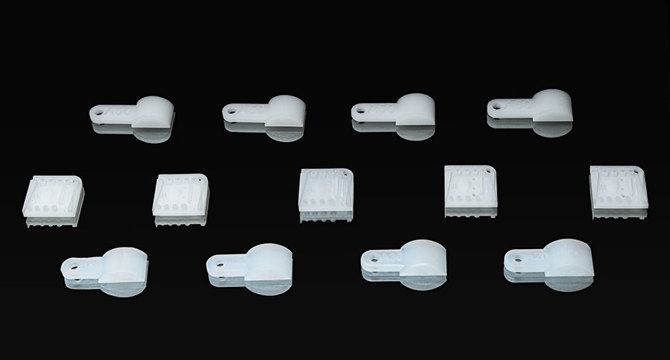
One of the principal features is the consistency of the LSR. For powerful 3D printing, the viscosity ought to be adequately low to flow flawlessly through the printer’s nozzle, guaranteeing even layer statement and solid layer attachment.
Curing time is another critical element. Quick curing LSRs are favored in light of the fact that they fundamentally decrease production time, considering quicker circle back in manufacturing. These sorts of LSRs cure rapidly upon exposure to intensity of heat or UV light, contingent upon the formulation. The capacity to change the curing system to fit specific production courses of events without compromising the material’s properties is fundamental for a productive work process and top quality results. A harmony between quick curing and adequate working time is important to guarantee accuracy in each layer before it sets.
The mechanical properties of the LSR, like elasticity, tear resistance, and stretching, are principal to the durability and usefulness of the printed objects. High elasticity guarantees that the printed parts can endure huge anxiety without breaking. Tear resistance is especially significant for applications including slim or many-sided designs, as it keeps the material from tearing during use.
Temperature resistance is another key component. The best LSRs for 3D printing can get through a large number of temperatures without degrading. This incorporates both high temperatures, which are normal in auto and modern applications, and low temperatures, which can be significant for specific electronic and clinical gadgets. A LSR that keeps up with its properties across these temperature limits guarantees reliable execution and life span of the printed parts.
Conclusion
Liquid Silicone Rubber has changed the scene of 3D printing, offering amazing flexibility, durability, and accuracy. Its exceptional properties make it reasonable for many applications, from medical gadgets to auto parts and customer hardware. By figuring out the advantages and elements of LSR, and knowing where to source excellent materials, makers and designers can use this inventive material to make progressed, custom items. As innovation keeps on advancing, the job of LSR in 3D printing is ready to extend, driving further development and conceivable outcomes in assembling and design.