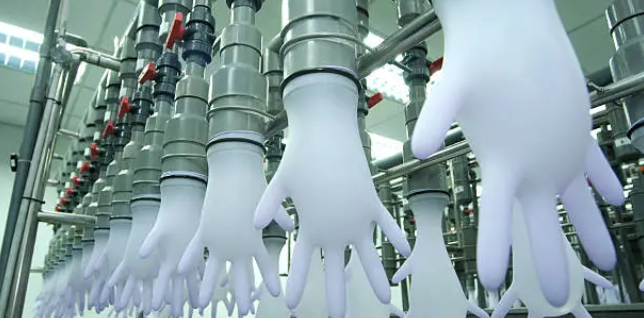
In the world of material manufacturing and use, liquid rubber and liquid silicone are versatile products that can be applied in a multitude of environments. Due to their distinct properties such as durability, flexibility, and temperature resistance, these materials are very popular across many industries. It is very important to have some insight into the versatility of liquid rubber and liquid silicone. We will also describe the process of making liquid silicone rubber and the applications that it has. Understanding the various uses of these polymers will reveal their function carried out in the various applications.
What is Liquid Rubber Used for?
Liquid rubber is actually a generic term that encompasses many elastomer coatings and sealants. These materials are normally in the form of a liquid that hardens to form a flexible rubber kind of layer. Here are some common ways liquid rubber is used:
- Waterproofing and Roofing: the most important function of liquid rubber is as a coating in waterproofing. It continues to be utilized in the sheathing of roofs, basements, and foundations to shield them from water seepage. Due to the nature in which it can form a strong and seamless layer, it is well suited for use when protecting structures from moisture.
- Protective Coating: liquid rubber can also be used to give a covering to wood, metals, and concrete. It is useful in avoiding corrosion and other adverse effects from the surroundings, hence extending the durability of these materials.
- Automotive Industry: liquid rubber is applied to the undercarriage of cars in the automobile production process. This helps guard the vehicles against rust and other hard materials on the roads, such as stones, among others. It is also applied in the manufacturing of automobile components such as seals and gaskets
- Recreational Applications: Due to the high resistance to UV rays as well as saltwater, liquid rubber is more suitable to be used in boats, docks, and swimming pools. The protection it offers can be lasting given that it is resistant to damaging environmental factors.
- Industrial Applications: in industrial segments like mining and manufacturing sections, liquid rubber is applied as a coating to preserve the equipment against deterioration. Using the material on the belts, pipes, etc, cuts down the probability of contact with rough materials.
What is Liquid Silicone Used For?
Taking advantage of silicone’s many defining characteristics, it can be utilized in a multitude of environments. Here we have some of the most common applications:
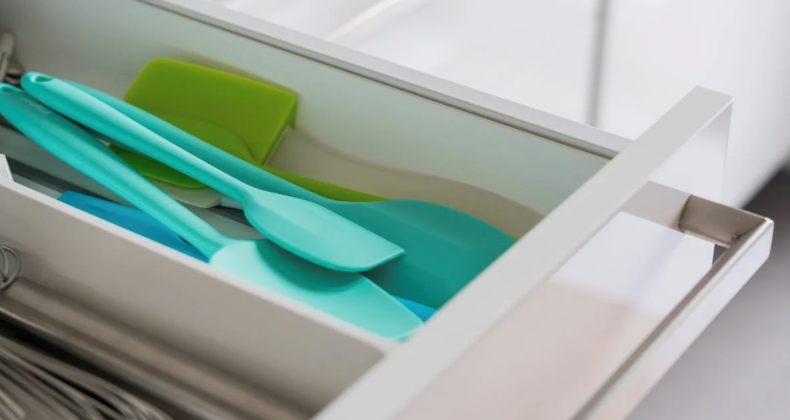
- Medical Devices: due to its biocompatibility, liquid silicone can be used in various ways in the medical field. t is used to make medical devices such as catheters, respiratory masks, and implants. Silicone’s non-reactive nature makes it ideal for applications where extended body exposure is involved.
- Consumer Products: kitchenware such as baking molds, spatulas, and ice cube trays are regularly made using liquid silicone. Its resistance to extreme temperatures and non-stick characteristics make it right for these products.
- Electronics: silicone is primarily used as a protective coating for sensitive components in the electronics industry. It helps to insulate the parts and protect them against moisture and rust.
- Automotive and Aerospace Industry: some of the uses of liquid silicone include the manufacturing of automobile and airline industries mainly in the production of seals and gaskets. These components are exposed to high temperatures and other difficult conditions and, therefore, depend on the properties of silicone.
- Cosmetic Industry: liquid silicone is applied in the beauty and personal care industry very frequently. It is applied in merchandise such as compact powder pads, facial massagers, and other skincare accessories as it is soft and flexible, hence skin-friendly.
What is Liquid Silicone Rubber?
Liquid Silicone Rubber (LSR) is the latest type of silicone polymer manufactured with the assistance of a platinum catalyst. The material is popular because of its excellent flexibility, strength, and heat-proof characteristics. In contrast to the standard polymers, such as rubber or silicone, LSR does not experience changes to its characteristics or destruction at large temperature intervals. This makes liquid silicone rubber the most suitable choice for those applications in areas that experience high stress
LSR is usually available as a two-component kit which you combine and cure to get the final product. The curing process involves the use of heat, which causes the material to solidify into a flexible, rubber-like state. Curing can be carried out in mold to get the precise form you desire.
What is Liquid Silicone Rubber Used for?
Liquid silicone rubber has many defining attributes, from its durability to its chemical resistance, that make it the right choice for various sectors. Let’s look at the different ways you can take advantage of these qualities:
- Medicine and Healthcare: LSR is constantly used to manufacture medical components such as seals and diaphragms. Its biocompatibility and ability to maintain its integrity through multiple sterilizations are very useful in this regard.
- Consumer Electronics: silicone rubber liquid is used to manufacture some of the electronic device’s components such as buttons and keypads. This makes it useful because it is both strong and can bend.
- Household Goods: in addition to cooking utensils, liquid silicone rubber also produces nipples for baby bottles, pacifiers, and toys. In this respect, it does not cause an allergic reaction or cause damage when put into contact with either skin or food.
- Industrial Applications: further found in industrial environments is LSR, which is used in making tough molds, gaskets, and other parts.
- Mold Making: Silicone has very little rigidity and captures tiny details well enough. As a result of its flexibility, silicon becomes useful for casting materials like resins and plastics.
How Silicone Rubber is Made
The process of manufacturing liquid silicone rubber is a detailed one and involves several steps. Here are the steps involved in the manufacturing of silicone rubber:
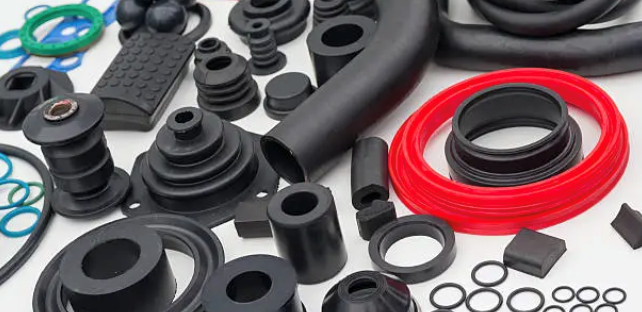
- Synthesis of Siloxane: it all begins with siloxane. This substance is formed through the combination of carbon, silicon, oxygen, and hydrogen.
- Polymerization: with continuous polymerization, siloxane gets converted into polydimethylsiloxane, which forms the basic component for making silicone rubber.
- Compounding: to enhance its properties, fillers, stabilizers, colorants, and other additives have to be added to polydimethylsiloxane. Thus it tailors it depending on its specific use as a form of silicone rubber.
- Cross-linking: a platinum-catalyzed reaction is used for cross-linking the compounded mixture. This creates a three-dimensional structure that gives silicone rubber its elasticity.
- Molding and Curing: the cross-linked silicone rubber is shaped into the needed shape before it is cured to finalize its form.
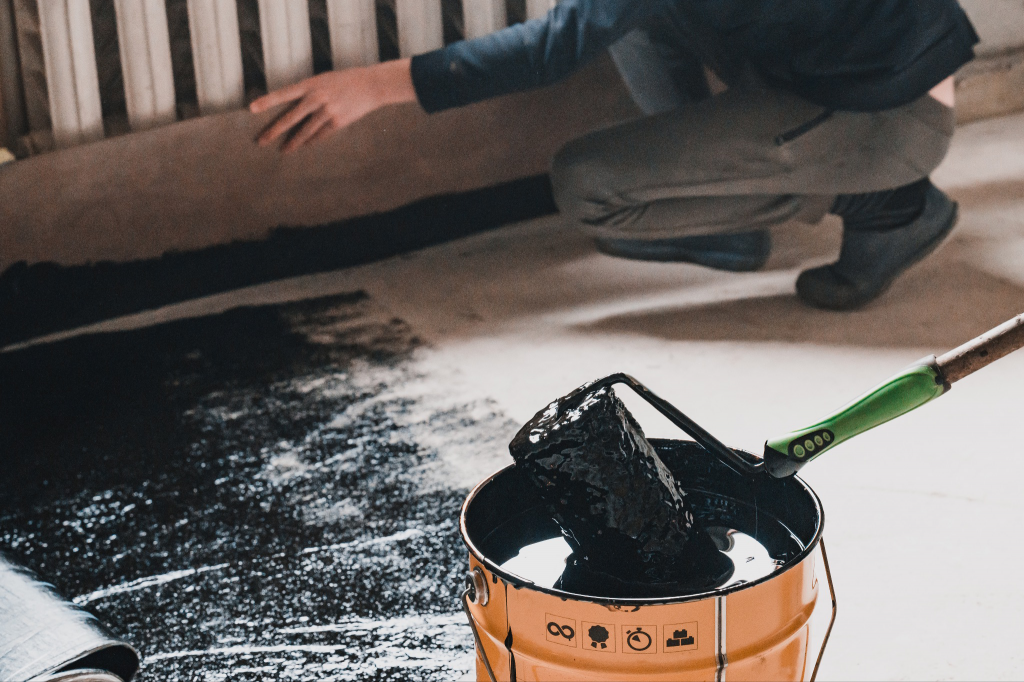
Insilicone: The All-rounder for all Liquid Silicone Rubber Products
Insilicone leads in providing superior quality and dependable liquid silicone rubber products. They have different types from babies’ goods to cookware or mobile phone covers. These quality products are available to you from the comfort of your home. Therefore, you have easy access to durable LSR products, especially for parents looking for the best baby products. You can also get stylish yet robust phone cases that will last you a long time. Their products have designs for everyday use along with options suited for more special occasions.
Conclusion
Due to their distinct qualities liquid rubber and liquid silicone are useful in a large number of sectors. These polymers are integral for waterproofing buildings to manufacturing medical devices and consumer electronics. These can never be done without due to their uniqueness, such as being able to resist both heat and being durable, among others necessary for modern life. Understanding their uses and how they are made reveals what are the best ways to apply them. As technology advances, the applications of these materials will continue to expand, highlighting their importance in our daily lives and industries.