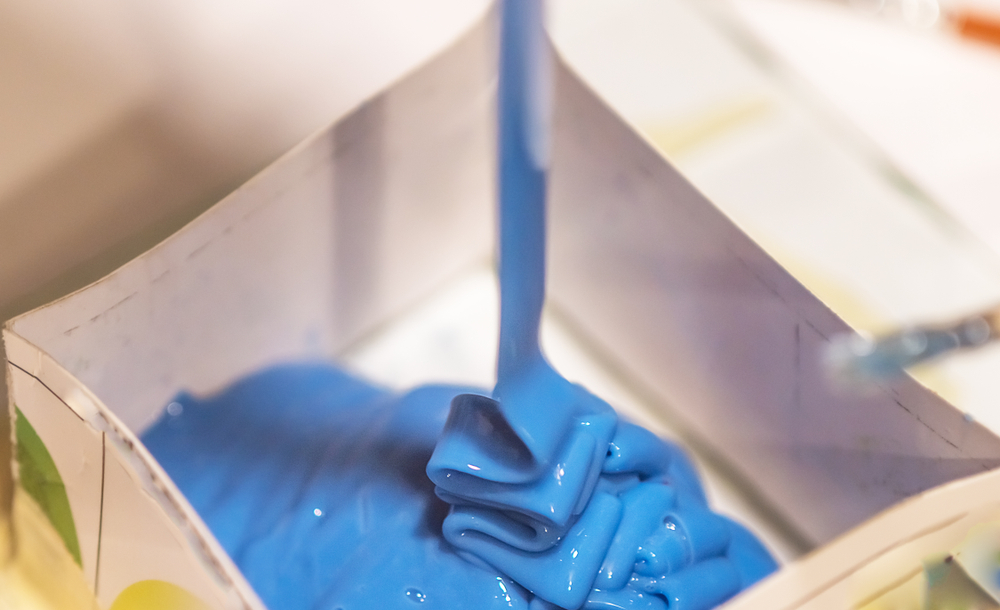
Liquid silicone rubber (LSR) is a flexible and solid material broadly utilized in shape-making. Its one-of-a-kind properties, like high flexibility, incredible thermal stability, and protection from mileage, make it ideal for making definite and complex molds. This report dives into different parts of liquid silicone rubber for molds, including its sorts, contrasts from other silicone rubbers, and the shape-making process.
Liquid silicone rubber for mold making
Liquid silicone rubber is a two-part material that, when blended and cured, changes into a flexible yet solid shape. It is especially preferred for applications requiring high accuracy and fine details. Here are a few key qualities that make LSR reasonable for shape-making:
- Flexibility and Strength: LSR can stretch and curve without tearing, ensuring the form holds its shape for different purposes.
- Heat Resistance: It can endure high temperatures, making it appropriate for casting materials like resins, metals, and, surprisingly, a few plastics.
- Chemical Resistance: LSR is resistant to numerous chemicals, decreasing the risk of shape-changing after some time.
- Non-Toxicity: Being safe for food items, it’s frequently utilized for molds in culinary applications such as baking trays or freezing molds.
The mold-making process includes a few stages, beginning with the planning of the model and finishing with the curing of the silicone. The mold is tough, reusable, and fit to create detailed imitations.
What is the difference between liquid silicone and silicone rubber?
Understanding the differences between liquid silicone rubber (LSR) and traditional silicone rubber is critical for choosing the right material for your projects. Here are some characteristics needed to judge a suitable type of silicone rubber:
Form and Consistency
Liquid Silicone Rubber (LSR):
- Liquid Consistency: LSR has a low thickness, making it pourable. This fluid nature licenses it to stream into complex nuances and catch fine features of a model.
- Two-part system: Consistently, LSR is a two-part system that should be blended before use. The two parts answer the structure’s serious areas of strength for rubber.
Traditional Silicone Rubber:
- Exceptionally viscous: Traditional silicone rubber can go from thick glue to strong design. It isn’t exactly as flowable as LSR, which makes it less appropriate to cut out fine details.
- Single or Two-part: It can come as a one-part material that cures upon receptiveness to air or moistness, or as a two-part system like LSR anyway with higher consistency at the beginning.
Curing Process
Liquid Silicone Rubber (LSR):
- Room Temperature Vulcanization (RTV): Liquid silicone rubber as often as possible cures at room temperature, which is beneficial for certain applications. In any case, the curing period can be progressed rapidly with heat.
- Catalyst-Driven curing: The curing system is driven by a catalyst, ordinarily platinum-based, guaranteeing a thorough and even cure.
Traditional Silicone Rubber:
- Room Temperature Vulcanization (RTV): RTV silicones cure at room temperature, frequently utilizing a tin-based catalyst.
- High-Temperature Vulcanization (HTV): HTV silicones require high temperatures to fix, accomplished through a heating cycle. This type is utilized for applications requiring vigorous heat resistance.
Flexibility and Elasticity
Liquid Silicone Rubber (LSR):
- High Flexibility: LSR is profoundly elastic and can stretch essentially without tearing. This property is critical for molds that should be flexible yet tough.
- Detailed Replication: Its low viscosity considers catching complicated details, making it ideal for molds requiring high accuracy.
Traditional Silicone Rubber:
- Variable Flexibility: The elasticity of traditional silicone rubber differs depending upon its formulation. A few sorts are very flexible, while others are more inflexible.
- Less- detail-oriented: Because of its higher initial viscosity, traditional silicone rubber is less powerful at catching fine details than LSR.
Types of Silicone Rubber
Silicone rubber is a flexible material accessible in different forms, each customized to meet explicit industrial, medical, and customer needs. Understanding the various sorts of silicone rubber can assist you with picking the right material for your application, whether it’s for mold making, high-temperature conditions, or chemical resistance.
Room Temperature Vulcanizing (RTV) silicone
Room Temperature Vulcanizing (RTV) silicone is maybe the most generally used type of silicone rubber in mold making and prototyping. RTV silicone fixes at room temperature, making it advantageous for clients who don’t approach particular relieving hardware. It comes in two essential structures: one-part and two-part frameworks.
One-component RTV (RTV-1) silicone rubber fixes upon openness to air dampness and is frequently utilized for applications like curing, caulking, and covering because of its usability. RTV-1 silicones are regularly bundled in tubes and applied straightforwardly to the ideal surface, where they cure to form an adaptable rubber.
Two-component RTV (RTV-2) silicone requires blending two sections — a base and a catalyst— to start the restoring system. This type is especially well known in mold making since it offers more command over the restoring system and the last properties of the rubber. RTV-2 silicones are accessible in different hardness levels and can be planned to fix rapidly or gradually, contingent upon the particular application necessities. The capacity to catch fine subtleties makes RTV-2 silicone a number one in making molds for projecting soaps, waxes, and low-dissolving point metals.
Liquid Silicone Rubber (LSR)
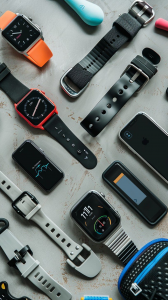
Liquid Silicone Rubber (LSR) is a profoundly flexible material known for its simplicity of handling and remarkable execution qualities. LSR is a two-part platinum-restored system that, once mixed and cured, turns into a flexible, solid rubber.
LSR is one of a kind since it begins as a liquid, allowing it to be injection molded with extraordinary accuracy. This makes it ideal for delivering detailed and complex parts that require fine detail. The injection molding process is profoundly automated, empowering high-volume production with reliable quality.
It is frequently used in applications like clinical gadgets, shopper items, and car parts. One of the champion elements of LSR is its biocompatibility. It is hypoallergenic and ok for direct contact with skin and mucous layers, making it appropriate for clinical and food-grade applications. Items like child bottle nipples, medical tubing, and wearable gadgets frequently use liquid silicone rubber.
Fluorosilicone rubber
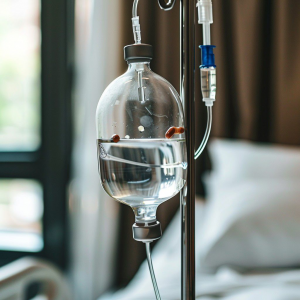
Fluorosilicone rubber is a specific silicone that integrates fluorine into its polymer structure. This adjustment improves its chemical resistance, especially to fuels, oils, and solvents, while holding a significant number of the beneficial properties of standard silicone rubber.
It is profoundly resistant to a large number of synthetic substances, including hydrocarbons, which makes it ideal for use in cruel conditions where openness to oils, fills, and different synthetic compounds is normal. This kind of silicone rubber is in many cases utilized in the aviation and car businesses, where parts should endure openness to fly fills, motor oils, and water-driven liquids.
However, its chemical resistance, fluorosilicone rubber, keeps up with its adaptability and execution over an expansive temperature range, like standard silicone rubber. It can work actually in temperatures from – 60°C to 200°C (- 76°F to 392°F), making it appropriate for applications that experience outrageous temperature varieties.
Silicone gels
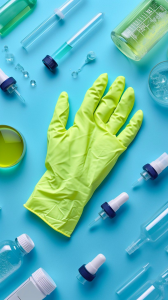
Silicone gels are a milder, more flexible kind of silicone rubber frequently used for padding and sealing applications. These gels are ordinarily used in medical and electronic industries because of their special properties. Silicone gels are very delicate and comparable, making them ideal for padding applications.
They are used in clinical items like wound dressings, prosthetic gadgets, and orthopedic cushions to give comfort and diminish pressure focus. The gel-like consistency permits them to adjust to the state of the body part they are applied to, offering predominant solace and security.
In gadgets, silicone gels typify and shield sensitive parts from dampness, dust, and mechanical harm. The gel’s capacity to stream and fill gaps guarantees total inclusion and security, while its adaptability permits it to absorb vibrations and mechanical stresses. This makes silicone gels ideal for safeguarding delicate electronic assemblies, connectors, and circuit boards.
High-Consistency Rubber (HCR)
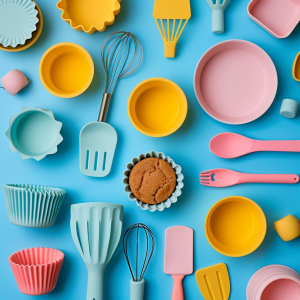
High-Consistency Rubber (HCR), also known as solid silicone. is a sort of silicone rubber known for its thick, gum-like consistency before curing. This type of silicone rubber requires high temperatures to cure and is handled using strategies, for example, pressure molding, transfer molding, and extrusion.
HCR offers astounding mechanical properties, including high rigidity, extension, and tear resistance, making it reasonable for requesting modern applications. Its capacity to endure outrageous temperatures, going from – 50°C to 200°C (- 58°F to 392°F), and its protection from ozone and UV radiations, make it ideal for creating auto parts, electrical insulators, seals, gaskets, etc.
Moreover, Its strength and flexibility guarantee that it keeps up with its performance in cruel conditions, giving reliable and enduring arrangements in applications where traditional rubber materials could fall flat.
How to make a mold out of silicone rubber?
Making a mold out of silicone rubber includes a few crucial steps toward guaranteed accuracy and strength. Here is a step-by-step guide:
- Choosing the Right Silicone Rubber: Select the fitting kind of silicone rubber in view of your project needs. For detailed and definite molds, LSR is normally the most ideal decision.
- Preparing the Model: Clean and set up the model you wish to imitate. Ensure it is free from any residue, dust and trash to precisely catch fine details.
- Building a Mold Box: Develop a mold box around your model. This box will contain the liquid silicone rubber and shape the mold.
- Applying a Release Agent: Apply a release agent to the model and mold box to keep the silicone from sticking.
- Blending the Silicone Rubber: Follow the maker’s directions to blend the two pieces of the silicone rubber completely.
- Pouring the Silicone: Gradually empty the blended silicone rubber into the mold box, ensuring it streams over the model and fills all gaps.
- Degassing the Silicone: If essential, use a vacuum chamber to eliminate any air bubbles caught in the silicone.
- Curing the Mold: Allow the silicone to cure for the suggested time. This could be a couple of hours overnight, contingent upon the type and thickness of the silicone rubber.
- Removing the Mold: Once cured, cautiously remove the mold from the box and separate it from the model.
Following these means guarantees that the subsequent silicone mold is accurate, strong, and prepared for re-use.
What kind of silicone do you use for molds?
The kind of liquid silicone rubber for molds used relies upon the particular requirements of the project. Here are a few elements to consider:
- Detail and Intricacy: For profoundly definite and complex molds, LSR is the most ideal decision because of its ease and capacity to catch fine details.
- Temperature Resistance: In the event that the mold will be presented to high temperatures, for example, for metal projecting, HTV silicone is more reasonable.
- Chemical exposure: For molds that will come into contact with harsh chemicals or oils, fluorosilicone rubber gives better opposition.
- Flexibility: Assuming the mold should be incredibly adaptable, silicone gels or gentler RTV silicones are fitting.
- Biocompatibility: For clinical applications, liquid silicone rubber is frequently liked because of its biocompatibility and security for use with skin and body.
Choosing the right sort of liquid silicone rubber for molds guarantees that the mold performs well under the planned circumstances and delivers excellent copies.
Conclusion
Liquid silicone rubber is an excellent mold-making material because of its flexibility, strength, and capacity to catch fine details. Understanding the differences between liquid silicone and traditional silicone rubbers, perceiving the different types accessible, and knowing the detailed steps for making silicone molds are fundamental for successful mold-production projects. By selecting the right silicone type and following the appropriate processes, you can make excellent molds that meet your particular requirements.