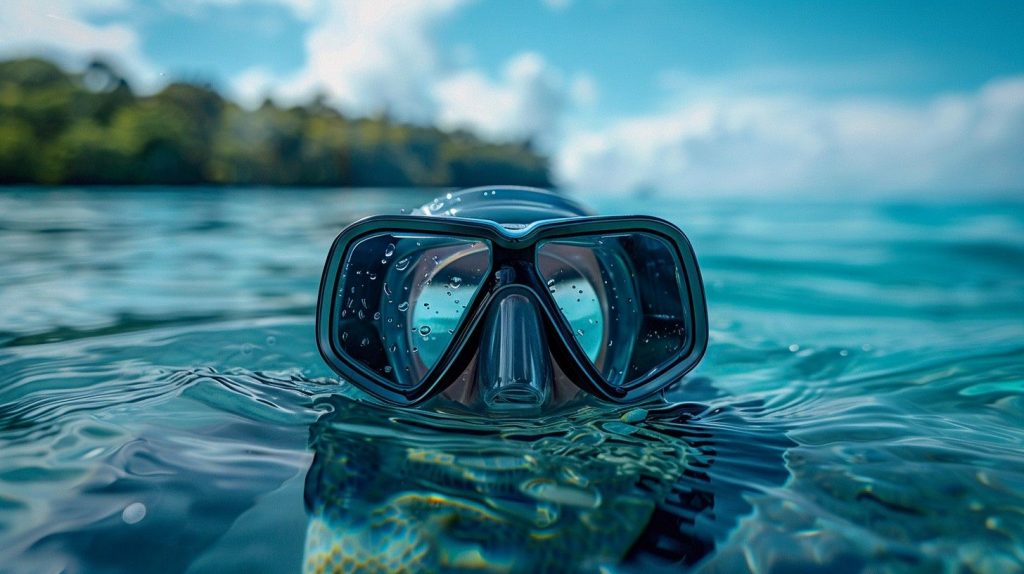
What continues the common section, i.e., medical implants, automotive seals, and cutting-edge electronics? A common factor in all of them is the advantages of Liquid Silicone Rubber (LSR) in terms of inimitable durability, flexibility, and heat resistance. This radical material is shaping the future of manufacturing let’s look into the reasons why!
However, what gives lifeblood to this material is the process of LSR injection molding, which is one innovation that delivers quality with unbeaten dependency.
In this blog, we take a look into the technosphere of LSR injection molding, discussing the sheer intricacies of the LSR molding process why LSR mold design is a vital purse string, and the way more updated advanced injection molding techniques are reshaping the ways industries create sophisticated LSR components.
The Magic of LSR: Why This Material Stands Out
Liquid Silicone Rubber (LSR) is a modern material of manufacture that contains unique combinations of properties with critical uses across different sectors. Its heat resistance, flexibility, and biocompatibility allow for manufacturing good components with precision and durability.
- Heat Resistance:
LSR can resist exceptionally higher temperatures with tremendous integrity and performance. This gives applications such as in automotive components like engine gaskets and seals that have to withstand higher temperatures for a considerably longer time without degradation.
- Flexibility:
The flexibility of LSR leads to complicated designs without much compromise on their integral strength. This then finds application in medical devices such as catheters and implants, where precision and durability become an utmost priority.
- Biocompatibility:
LSR is interestingly characterized by safety upon contact with the human body. Especially when meant for use for baby bottle nipples, surgical instruments, and prosthetics made under strict safety standards, it readily complies well.
Along with such advances in LSR i.e. Injection Molding processes. It offers extended applications. The advent of LSR injection molding has assured the production of precision-molded seals, gaskets, and components with definite geometries. So, this confirms the extensive applications it can find, especially, as seals and gaskets in the electronics industry.
Breaking Down the LSR Injection Molding Process
One prominent process is Liquid Silicone Rubber (LSR) Injection Molding: a precision-based approach to molding high-quality components using LSR. This makes for a highly efficient process with almost no room for error. Hence, the necessity in the healthcare, automotive, and electronics industries. The following provides a simplified description of the whole process:
- Material Preparations:
This is done with a two-part LSR compound mixture of the base material and curative. These could include colorants or stabilizers, depending on what is needed. Automated mixing is also used to enhance the process and eliminate human errors.
- Injection:
Using state-of-the-art LSR injection molding technology, the mixed LSR is injected into a pre-heated mold. Modern injection molding machines accurately fill even the most intricate designs, making it easier to reduce waste while improving the bottom line.
- Curing:
The curing process occurs inside the mold. Here, the application of heat transforms liquid silicone into a solid elastic material. Innovations such as close loops for temperature control and the optimized design of molds assist in uniformity of curing, even in unconventional and complex geometries.
- Demolding:
After curing, the part is carefully taken out of the mold. Automated demolding systems shorten cycle times and assure consistent quality by avoiding damage to delicate components.
Recent advancements in LSR injection molding include multi-cavity molds real-time monitoring and micro-molding technologies that enhance productivity and precision. Automation further streamlines the LSR molding process, making it much faster and cost-effective while still upholding phenomenal quality.
Game-Changing Advancements in LSR Mold Design
Some innovations in the LSR mold design have revolutionized the LSR molding process. These include increased efficiencies, sustainability, and accurate complex geometries. These advances are vital to such industries as healthcare, automotive, and electronics, where quality and uniformity are of extreme importance.
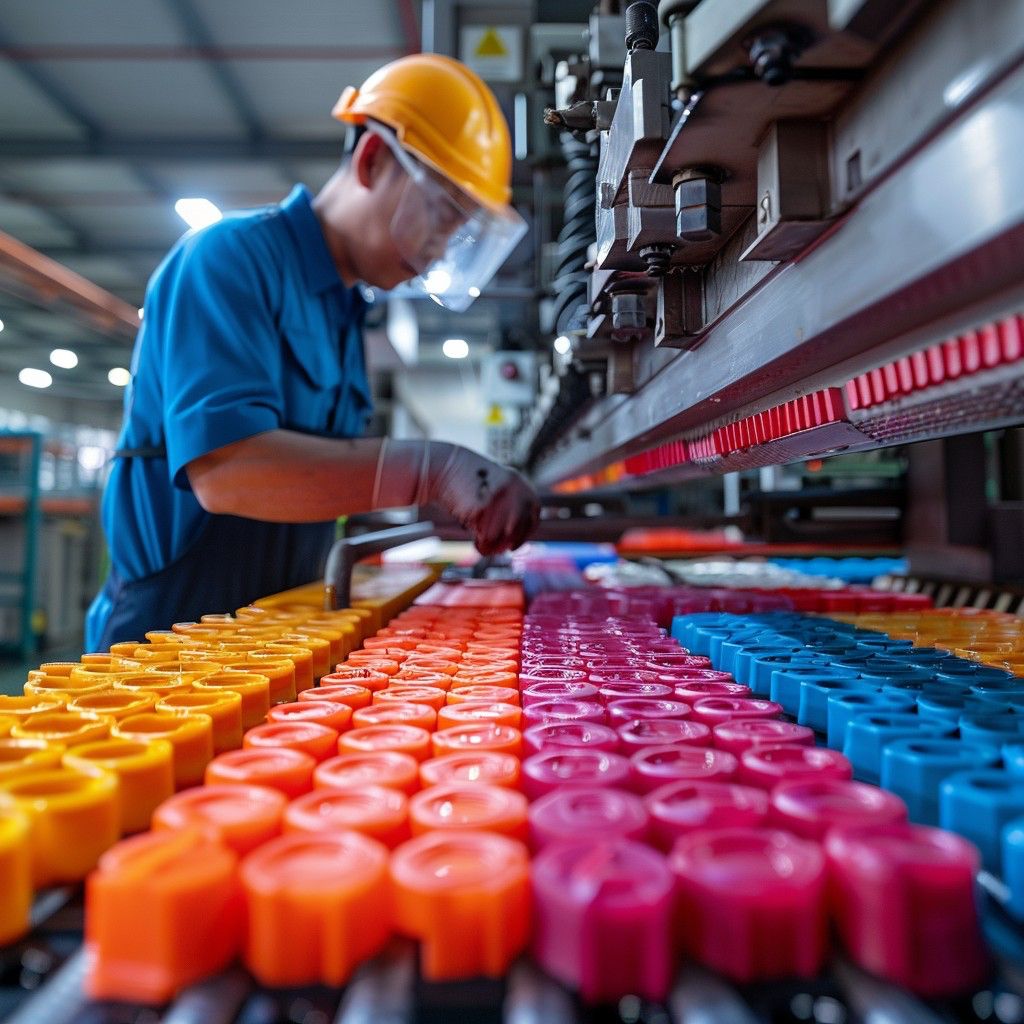
Multi-cavity molds, which allow for the simultaneous production of multiple parts, have been developed. This advancement improves production time more than anything else, along with lowering the cost while maintaining precision on complicated parts like medical implants and micro-electronics. Multi-cavity molds are used in the automotive industry to create seals and gaskets in high volume with the same constant quality.
Optimized cooling systems provide another great development. Manufacturers can achieve uniform curing and reduced cycle times by incorporating advanced cooling channels into mold designs. This is particularly advantageous in high-precision applications where temperature control is very critical, such as in the production of medical-grade tubing.
The CAD-driven approaches for mold creation have transformed the methods utilized in LSR injection molding. Wherein engineers, with the help of 3D modeling software, can design molds with complex geometries and simulate the injection molding process before actual production.
This ensures waste reduction and greater accuracy. For the same reason, CAD tools allow the design of over-molded components such as medical connectors that seamlessly combine different materials.
Advanced Injection Molding Techniques: Shaping the Future of LSR
Recent enhancements in LSR injection molding techniques have developed significant opportunities to manufacture precision components. These include micro-molding, two-shot molding, and over-molding, bringing a new revolution into LSR molding; through them, greater precision, efficiency, and design versatility are achieved.
Micro-molding:
This technique produces ostensible small and sophisticated parts with a level of tolerance tight enough to suit being used in industries such as health care and electronics.
For example, micro-molding is used in creating tiny medical components, such as microfluidic devices and implants that require superb accuracy and biocompatibility.
Two-shot molding:
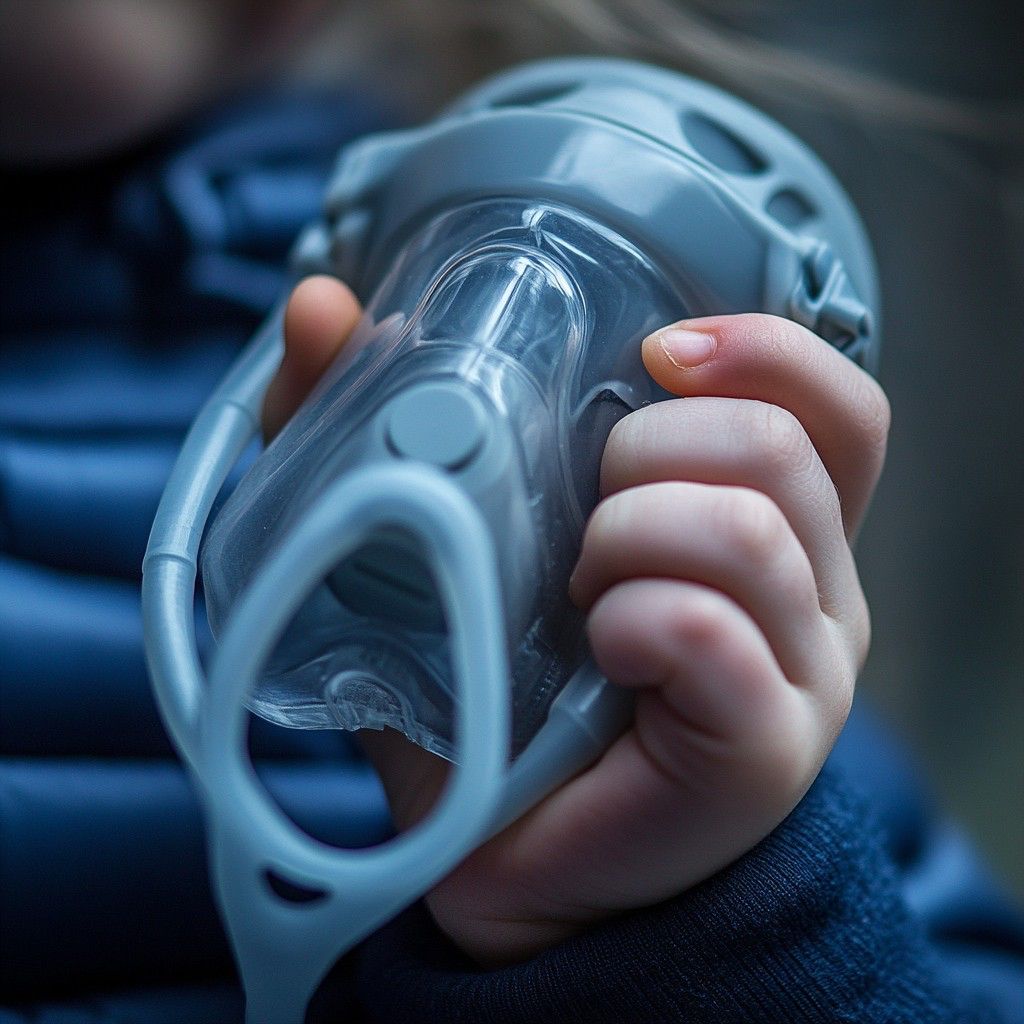
Two-shot molding allows for combining two distinct materials or colors in a single injection molding process. This way, materials with different characteristics could be combined with seemingly incompatible purposes. Such as making a part where the rigid and flexible sections can be combined. Most commonly, this is found in the production of ergonomic grips on surgical tools, where LSR material is used with hard plastics to increase functionality and comfort.
Overmolding:
Over-molding is a dual-layer built-in technique whereby LSR is applied over another material to leverage some performance or aesthetic characteristic. In the automotive sector, this is commonly used to make vibration-dampening seals or protective covers for electronic components to increase robustness and reliability in harsh environments.
The Road Ahead: Future Trends in LSR Injection Molding
Developments that the future holds in LSR injection molding could be, broadly, a revolution owing to these above-mentioned technologies and interest in sustainability.
Innovations such as AI-integrated quality control, sustainable practices, and hybrid manufacturing will, in turn, contribute to fresh perspectives surrounding the LSR molding process, improving horizons in several sectors.
AI-Driven Quality Control:
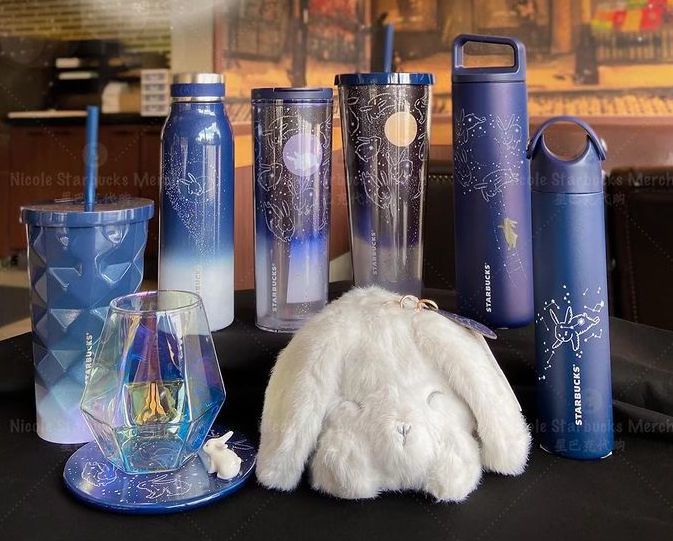
AI is bound to revolutionize the techniques used in LSR injection molding through live monitoring and defect detection. AI systems can analyze data such as those that will go into producing the items the quality of which needs to be checked.
They help ensure the quality of the molded products, minimizing cycle time, and recovering the molded material quite efficiently. In the case of medical device manufacturing, AI will enable us to achieve incomparable precision requirements for components like implants and catheters.
Sustainable Practices:
Sustainable solutions are the focus of every industry of the future, and LSR molding is no different in that regard. Material recycling innovation and energy-efficient molding systems will reduce the ecological burden. In addition to that, bio-based silicone materials for injection molding may provide green alternatives for production practices in industries such as healthcare and consumer goods.
Hybrid Manufacturing Techniques:
The blend of conventional LSR molding with methods of manufacturing that stress 3D printing will provide more freedom in design. These hybrid techniques can create intricate designs for LSR molds for components with complex geometries, such as wearable medical devices and advanced electronic seals.
InSilicone: Innovative Silicone Solutions for Tomorrow’s Industries
With our industry-leading LSR injection molding, custom silicone products, and precision-designed molds InSilicone is redefining innovation. Quality and technology are our mantra so you get only reliable high performing products that meet your needs.
Our custom silicone molding services cover a wide range of industries. Turn your ideas into real products today.
Advancing Excellence: LSR’s Journey Ahead
Continuous improvements in LSR injection-molding technologies are alive with precision, efficiency, and product quality. The evolution of LSR mold design and the optimization of the LSR molding process enabled the manufacturer to produce high-performance silicone components, and eventually, LSR injection molding became the favored choice among various other methods.
It finds its application in various fields from medical to automotive. LSR molding ensures greater durability, flexibility, and consistency even under the toughest conditions. With every changing day, as new techniques come into play, the future of LSR molding will be vibrant, proof of the changing trend in manufacturing.
Ready to elevate your next project? Book a call today or reach out to discuss your requirements! InSilicone is there for you and your silicone needs today and tomorrow!